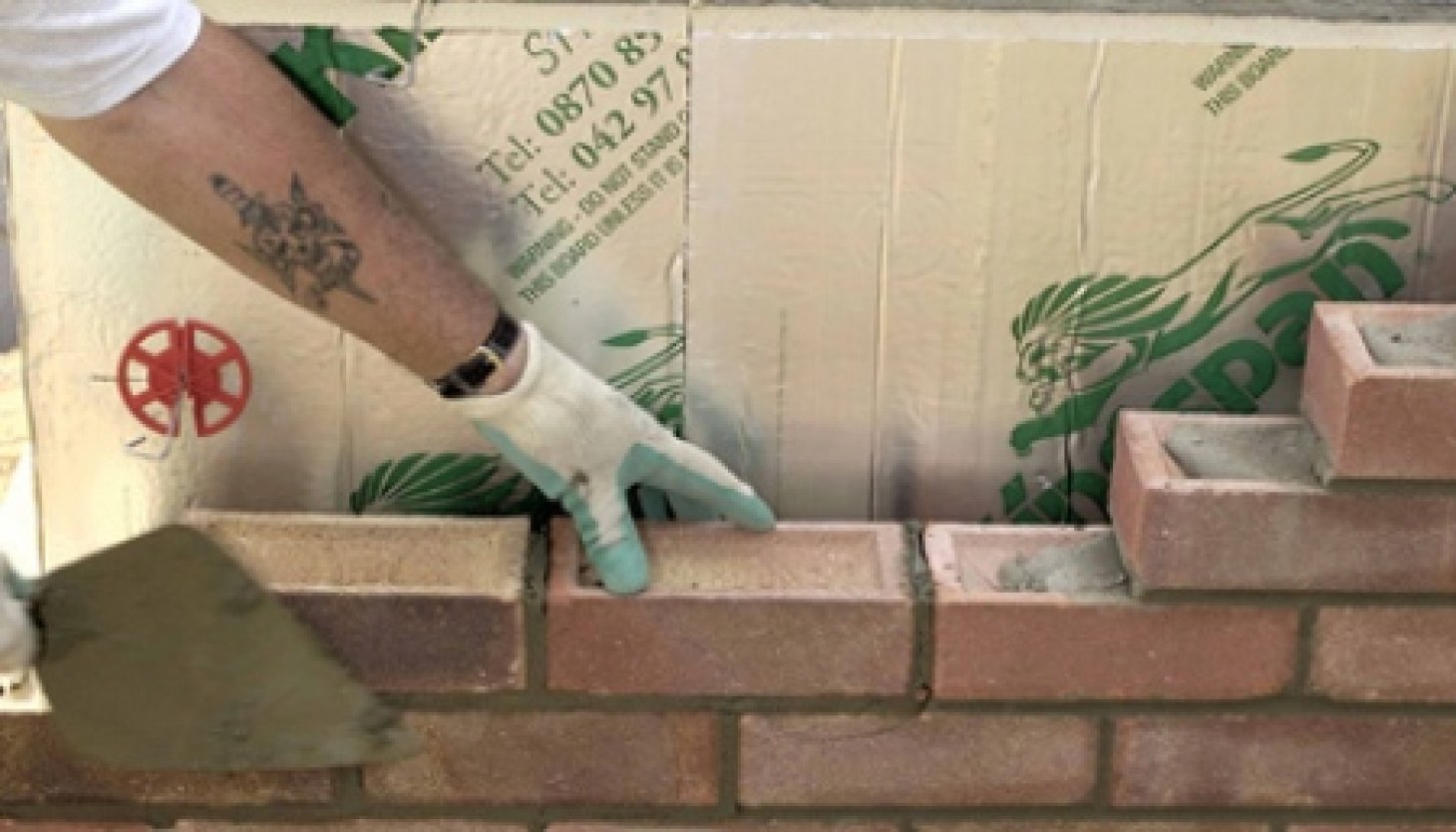
A Rå Build, thin-jointed solid wall aircrete masonry shell was the most cost effective solution for the Stondonfield social housing development in Essex. Principle Contractor Collins and Beckett looked at timber frame and off site methods before opting for H+H Hi-Seven 7.3N/mm2 Jumbo Bloks for the ground floor external walls of the 6 houses and 2 flats that make up the scheme.
These walls were then finished with either a LINAX timber board finish or rendered with a through coloured white Weber.therm XP External Wall Insulation System. A Lafarge Thermal Check K50 dry-lining system on dabs completed the walls internally and they achieve a U-value of 0.14w/m2K.
Being social housing, all the homes had to be built to level 4 of the Code for Sustainable Homes. This meant thermal and air tightness qualities of the build method would have to be excellent and speed of build was also key.
Mike Beckett, Managing Director, Collins and Beckett said: “By using thin-joint and a solid wall approach we were able to build extremely quickly and to very low U-values, enabling us to install whole house ventilation.”
He added: “This significantly reduces the amount of heat required to heat each dwelling, resulting in lower bills for the tenants. In fact, we needed no conventional boiler at all, each house requiring just 2 radiators.”
The Rå Build programme of aircrete wall construction took 9 weeks from start to finish, saving approximately 4 weeks when compared with a traditional masonry build. All the dwellings are now fully occupied for client Circle Housing Group