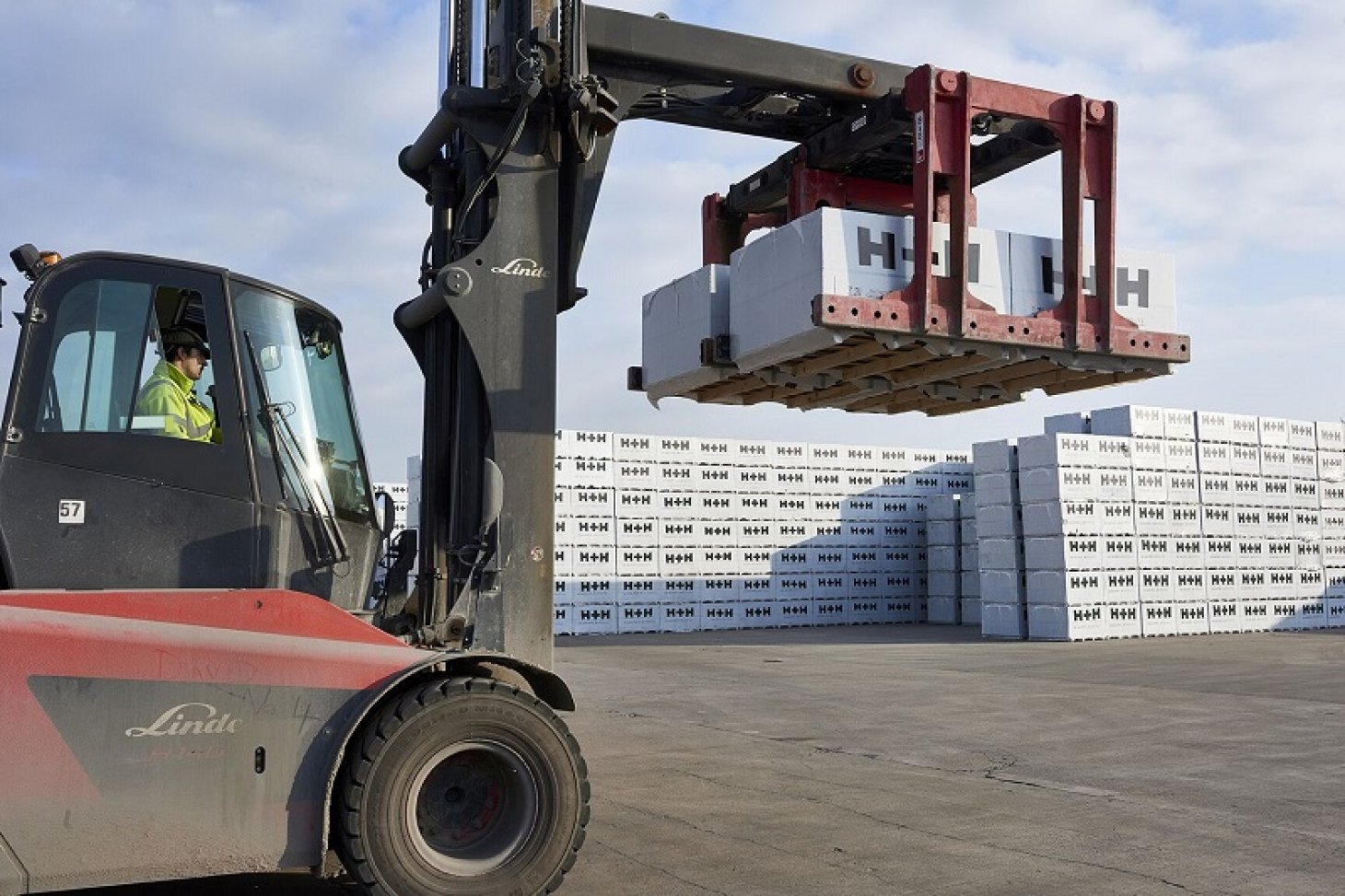
Working at height is always a potential danger point, and the team at our Pollington plant have taken some radical action to reduce risk.
HSE figures suggest that the most dangerous point of any product haulage process is the loading and unloading of vehicles. It’s a widely recognised problem, with statistics suggesting that some 250 people suffer significant injuries each year as a result.
The team at Pollington decided that it was time to entirely redesign our loading procedures to eliminate this risk as far as possible. We see it is our responsibility to ensure that all visitors to our site are safe.
It may sound like a minor change, but in fact it is anything but. Challenging long-established routines and asking people to change familiar behaviours takes tact, time and commitment.
Visitors to the yard will immediately notice the difference as there is a strict one-way system and the routes for delivery vehicles are now completely separate to those used by cars.
Traffic flow is important, but the major risk occurs when people climb onto lorries during loading. Understanding just why this happened needed a thorough examination of the packing and stacking procedures.
From that point a new method of loading the lorries was designed, in close co-operation with our haulage company and with the HSE to make sure that Highways England were happy with the safety of the new loading systems.
It’s one thing to introduce a new procedure and quite another to make sure it sticks. New signage in the yard, including detailed diagrams of stacking procedures, is very evident and a drivers’ handbook has been placed in every lorry that visits the H+H yard.
Three months into the reorganisation and the yard is looking more orderly than ever. Waiting times are dramatically reduced as the new system is much more efficient but, most importantly, we are demonstrating our commitment to ensuring the safety of both our staff and our visitors.