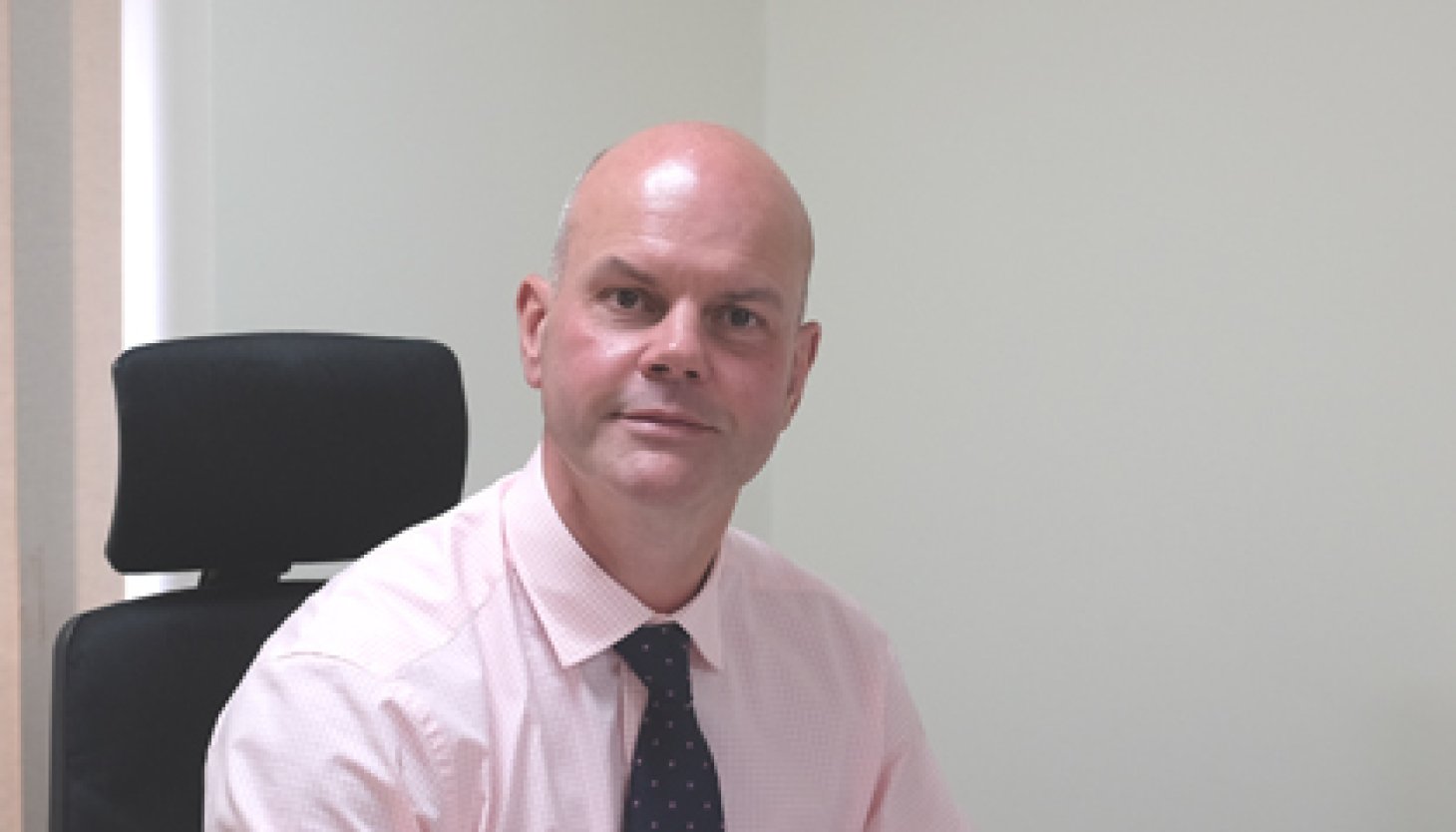
H+H is facing the uncertainties around the Brexit referendum with a resounding vote of confidence in the UK market. The decision to go ahead with a multi-million pound investment in our Borough Green factory has been confirmed and we are forging ahead with some genuinely ground-breaking product innovations.
The investment in our factory will effectively replace the main production facility, allowing us to capitalise on more modern technology, increasing the production capacity and also improving the consistent quality of the blocks produced at the plant.
Contracts have been signed with the equipment manufacturers and we will spend the next 15 months preparing for the transformational build which is scheduled to take place during the winter of 2017 / 2018.
In making this investment, our parent company is expressing its confidence in the strength of the market in the UK. We can see the continued demand for new housing, and as housebuilding moves ever further up the government agenda there is reason to be confident that the volume of housebuilding will continue to increase.
Question marks over the ability of the current labour market to actually build the number of homes being mentioned in government targets is leading to renewed interest in offsite manufacturing and at H+H we are meeting this opportunity with innovations designed to reduce site time.
We are currently working on the development of a Vertical Elements System which will be an entirely new concept for building in aircrete: a complete building package intended for the construction of low rise domestic houses.
At its core, the system will use storey-high panels of aircrete. Lifted into place using a crane, the vertical joints will be filled with a fast setting thin-joint element mortar which has been specially developed for use with the elements.
Combined with prefabricated timber floors, Vertical Elements allow for the weatherproof shell of a two-storey house to be completed with maximum efficiency: All components of the construction are lifted into place by crane providing a consistent quality of build with minimal site labour.
This is a radical step forward: it builds on the experience we have gained working with the Vertical Element panels – originally trialled in the UK just before the economic downturn and used successfully across Europe to reduce build times – and fits them into a complete system-build offer.
Planning is at early stage, but we see this as a way to capitalise on the performance benefits of aircrete while meeting a demand for short site time and minimal site labour.
A move to any kind of offsite construction requires a complete re-think of the way site are staffed and managed. We believe that while offsite will provide a practical solution for some larger contractors the majority of houses will continue to be built using traditional methods for many decades to come.
This does not mean that innovation cannot improve traditional build, however, and our thin-joint method, offering major time savings and the improvements to airtightness that are important for high-performance building methods such as passivhaus, remains high on our agenda.
New training packages, our in-house estimating and design service and an investment on our promotion to architects and custom build proponents will see sale of this innovative system continue to grow.
In short, while some sectors of the construction industry seem to be entering a potentially dangerous hesitation in response to Brexit, we are taking the opposite view and making key decisions that will ensure the future of H+H and aircrete products into the next decade and beyond.