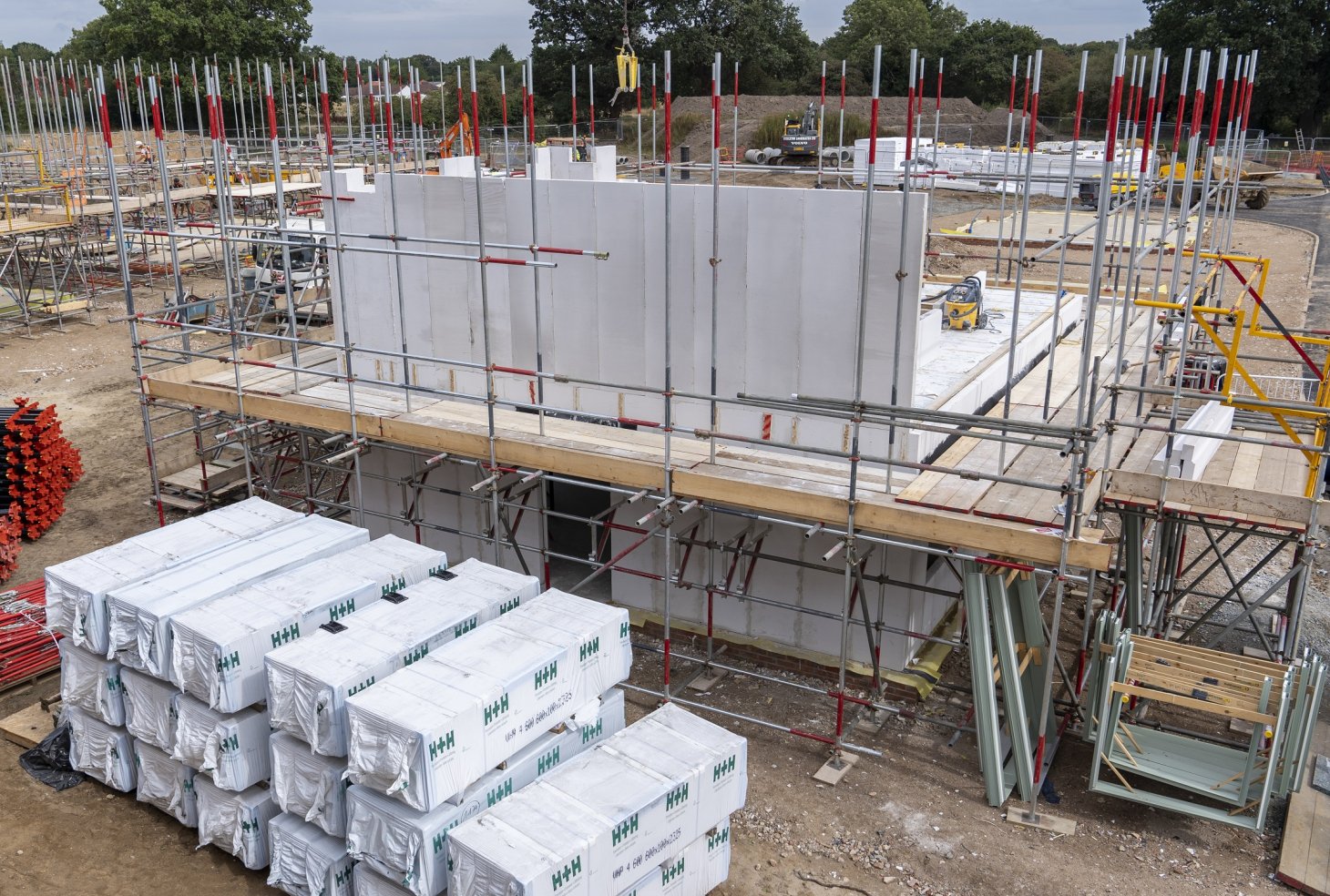
The Construction Industry Training Board (CITB) has revealed a huge deficit in the number of construction workers needed over the next 4 years in its annual industry forecast.
Construction output rose by 2% in 2023, the third consecutive year of growth. Continuing this trend, the industry is expected to grow by an average 2.4% a year between now and 2028, requiring over 250,000 extra construction workers to meet the forecasted demand. This would bring construction employment to 2.75 million workers and increase the need for training to accommodate the variety of skills required.
Despite the construction industry recruiting around 200,000 people annually, it loses even more, with 210,000 workers leaving each year, and an average of 38,000 vacancies advertised per month in 2023. This ongoing gap between the predicted need for construction work and the available workforce is an increasingly urgent issue which needs to be addressed.
For nearly a third of construction employers, the primary challenge remains finding suitably skilled staff, especially as more older workers retire without sufficient replacements. In addition, the increase of Modern Methods of Construction (MMC) is leading to a demand for new skillsets. According to the CITB’s forecast, effective training is crucial for replacing those leaving and better preparing for the future.
While recruiting and training more construction workers is imperative, the use of MMC is helping to ease the strain of future demand, as it often requires fewer site workers and means projects can be completed more quickly, with more built as a result.
One example of an MMC solution which offers both of these benefits is H+H Vertical Wall Panels (VWPs). VWPs are storey high aircrete panels that offer an alternative method of housebuilding to traditional brick and block while maintaining the same high performance of aircrete.
H+H Vertical Wall Panels are quick to install, with the entire ground floor of a house able to be installed in just one day. The panels are craned into place on standard foundations and secured with fast-setting strong mortar. When combined with prefabricated timber floors and roof joists, the system enables the shell of a house to be built in as little as five days.
With a little training, those with experience of building with traditional methods, for example carpenters who install timber floor cassettes and roof joists, can easily learn to install the VWP system. In fact, H+H offers this training for free. These additional skills enable site workers to take on a wider variety of projects without having to take time out to undergo extensive training.
One housing provider which has embraced the Vertical Wall Panel system is Abri. Having committed to delivering 25% of its homes using MMC Categories 1 or 2, Abri has chosen to construct affordable homes with VWPs at its Sherecroft Farm site in Hampshire. Jake Snell, Head of Partnerships & Innovation at Abri who was instrumental in the decision to transition from traditional building methods to VWPs, comments:
“We investigated various MMC products to find the best fit for Abri. When we were introduced to H+H and its Vertical Wall Panel system, we realised it was a game changer.
“Adopting a new build method is a major cultural shift for both our on-site teams and our back office. The Vertical Wall Panel system is an ideal solution as it comprises a familiar material in a more advanced product. It lets us adapt our culture rather than creating a new one and the system significantly reduces the level of risk compared with innovation used in other construction techniques.”
To read more about the Abri Sherecroft Farm build read the full case study here or to find out more about Vertical Wall Panels visit our VWP product page.