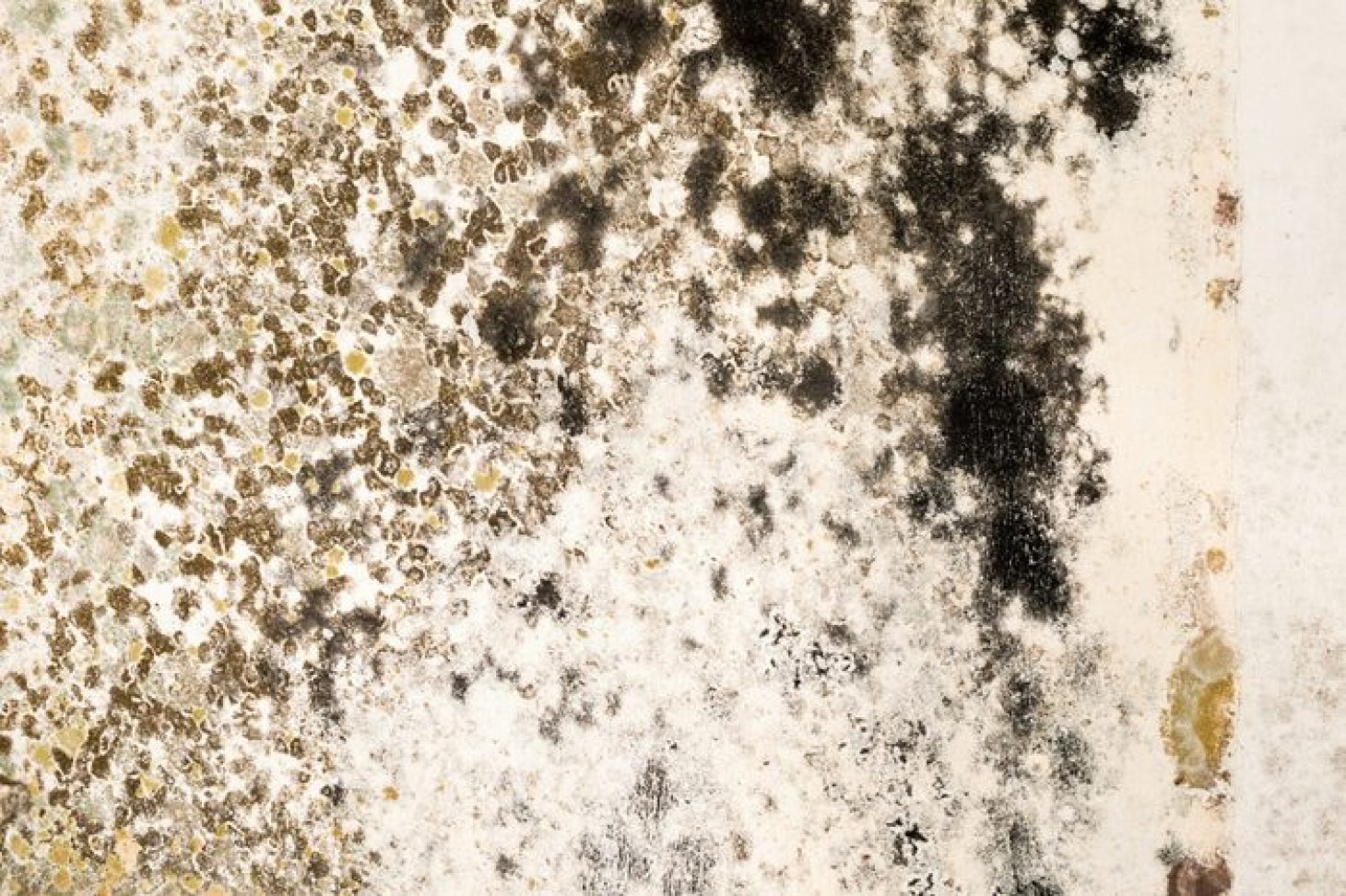
Modular building has been in the news for all the wrong reasons recently as problems with mould hit L&G modular homes under construction in Bristol and North Yorkshire.
The last few years have seen offsite construction placed high on the housebuilding agenda, with Homes England stipulating that at least 25% of homes delivered through its Affordable Homes Programme should be built using MMC.
But have we done our due diligence? How durable are modular homes and does this recent issue call into question the fundamentals of offsite construction?
Modular construction
Modular homes are prefabricated homes that are constructed off-site, in a factory, as ‘furnished’ sections or modules that are delivered to site and fitted together to form complete buildings.
These modules are transported to site on the back of a lorry and are usually too large to cover efficiently, so for the duration of the journey they are exposed to the elements. Once on site they often remain exposed until the building is made completely weathertight.
At any point in the process while modules are waiting to be shipped, being transported or are on site before they are made weathertight, they are at risk of being exposed to moisture.
It has been reported that the mould problems with the L&G units developed while the factory-built homes were being stored ahead of installation on site. L&G has commented that it is ‘incorporating lessons learnt into its storage process’. However, the question remains whether the opportunity for prefabricated units to get damp can ever be completely eliminated.
Prefabricated units are usually constructed from timber and furnished with insulation and plasterboard on the internal walls before being shipped to site. Unlike with masonry, once moisture has penetrated these materials there is a risk of rot or mould developing, which can be extremely difficult to remove.
The problem with moisture
The seriousness of mould growth must not be underestimated, as we saw with the tragic death of Awaab Ishak in 2020 who died as a direct result of black mould in the flat he lived in.
Damp and mould are some of the biggest issues currently faced by social housing associations with the number of social housing tenants in England complaining of damp and leaks on course to more than double in the years since Awaab’s death.
With damp a prevalent issue with existing social housing stock, it is imperative that we avoid building this same issue into brand new housing.
It is not only the storage and transportation of modular buildings that needs to be reviewed to reduce risk of exposure to moisture. Interstitial condensation is another issue to consider.
Within traditional construction, interstitial condensation in buildings is less able to cause damage as water forming on a block or brick, while not good, will not cause structural damage and can be easily rectified should it occur. However, moisture forming on a light gauge steel or timber frame could lead to corrosion or rotting and ultimately the failure of the structural frame.
Building warranty suppliers now ask for additional proof that interstitial condensation is not a factor in MMC as the consequences with a timber or light gauge steel frame could be catastrophic. As such there is a move to carry out more physical testing of the condensation risk rather than relying on computer modelling which doesn’t necessarily mirror real life conditions.
Building safety
While it is the issues with mould that have led to prefabricated homes hitting the headlines most recently, other building standards must also be considered in relation to modular building.
In December, the National Fire Chiefs Council voiced its concern over whether the desire to build homes quickly and sustainably using MMC was being prioritised at the expense of building safety. It warned that there was ‘significant uncertainty’ over the fire performance of modular homes, calling for stricter testing.
This followed concerns raised over the fire safety of modular buildings after a fire destroyed the Moorfield Hotel in Shetland in July 2020. The hotel had been constructed offsite as fully furnished modules and assembled on site. A similar process was used to construct the Fair Isle Bird Observatory in Shetland which was also destroyed by a fire, in 2019. Both fires were reported to have grown quickly with fire crews unable to stop the spread.
According to experts interviewed by the BBC in relation to the Shetland fires, more investigation is required into modular buildings and their construction with questions over firebreaks and their installation, combustible materials being used in cavities and the general compartmentation practices involved.
This was echoed by Ron Alalouff, a journalist specialising in the fire and security markets, who highlighted concerns in an article for IFSEC Global about the fire performance of MMC. These included that where components are fixed together, there may be hidden voids through which smoke and hot gasses can travel through a building.
Building for the long term
Prefabricated housing certainly fits the brief in terms of building more homes more quickly, but how durable are they? Are we storing up problems for ourselves in the long term?
Homes constructed of masonry, whether traditional blockwork or using MMC methods, have a life expectancy of over 150 years whereas the modular homes built in the UK today are only designed to last for 60 years.
Prefabrication methods were used to build new homes quickly between the end of the Second World War and the late 1970s. Much of the UK’s current social housing was built during this period with these methods and is now coming to the end of its lifespan.
Following a series of media reports revealing appalling levels of disrepair in some social housing, the Levelling Up, Housing and Communities Committee launched an inquiry into the regulation of social housing in November 2021. The inquiry found that one of the principal causes of housing disrepair is the age and design of the social housing stock. This highlights the importance of building durable homes that will last for generations to avoid a repetition of these issues in 60 years time.
Does it make sense to build today’s much needed new homes to have a short life expectancy? With 35 and 40 year mortgages becoming more common shouldn’t a home be designed to last for more than one mortgage term? At the end of the third quarter of 2022, half of all first time buyers and a quarter of all home owners took out mortgages over a 30-year term. This compares to about a quarter of first time movers and 10 per cent of homeowners in 2012.
Certainly, modular homes are still regarded as ‘non-standard properties’ by mortgage lenders making the process more complicated and potentially more expensive for homeowners.
According to insurance specialists, GoCompare the same applies when insuring a modular home. There are likely to be fewer insurance companies willing to cover a property of non-standard construction and premiums may be higher because repairing or replacing parts of the home is likely to be more complicated, time-consuming and expensive.
Modular and prefabricated homes are not the only answer to the current housing shortage and to overlook more reliable, tried and tested methods such as masonry build, for which there are also MMC solutions, may be a costly oversight.